We continue the previous article's backflush discussion with a description of the most common form of backflush: post-column backflush.
Of the three possible configurations of capillary column backflush (post-column, coated re-column and uncoated pre-column), post-column is the most straightforward. Figure 1 illustrates a schematic for typical post-column configuration.
Advantages of the post-column backflush configuration
- It is the easiest mode to understand and implement; backflushing is very simple
- Immediately after the last component of analytical interest elutes (obvious from the chromatogram), data acquisition ends, (if used, MS source is turned OFF) and backflush is initiated
- Temperature is held at the elution temperature of the last compound of interest (the original temperature program is modified), improving cycle times both on heat-up and cool-down
- The determination and verification of backflush timing is the easiest of the three approaches - The analytical column is one single unit with constant mass flow through its full length
- no degradation in original separation efficiency
- no intermediate connections
- original column remains intact - It is possible to very precisely cut between two closely eluting peaks (e.g., if the later one might be harmful to the detector)
- Does not prevent use of pressure pulsed injections (sometimes used to allow large injection volumes and to decrease degradation of labile compounds)
- Retention time locking [1] implementation is very straightforward and rugged to apply
Disadvantages of the post-column backflush configuration
- Flow is added to the column effluent
- The choice of device pressure, restrictor dimensions and temperature dictate the flow rate to the MS or GC detector(s)
- Even a prudent choice in restrictor can reduce mass spectrometer sensitivity 15-20%
- Larger than necessary i.d. (bad choice in restrictor) can decrease sensitivity and S/N of a mass spectrometer much more dramatically - Most tubing used as restrictors is deactivated but uncoated, as such it is more active than coated analytical columns and there is a possibility of increased loss of labile compounds.
- Due to high flow rates through the post column restrictor during backflush, the post-column configuration is not suitable when using flow limited detectors (e.g., diffusion pump mass spectrometers) or flow sensitive detectors (e.g., NPD)
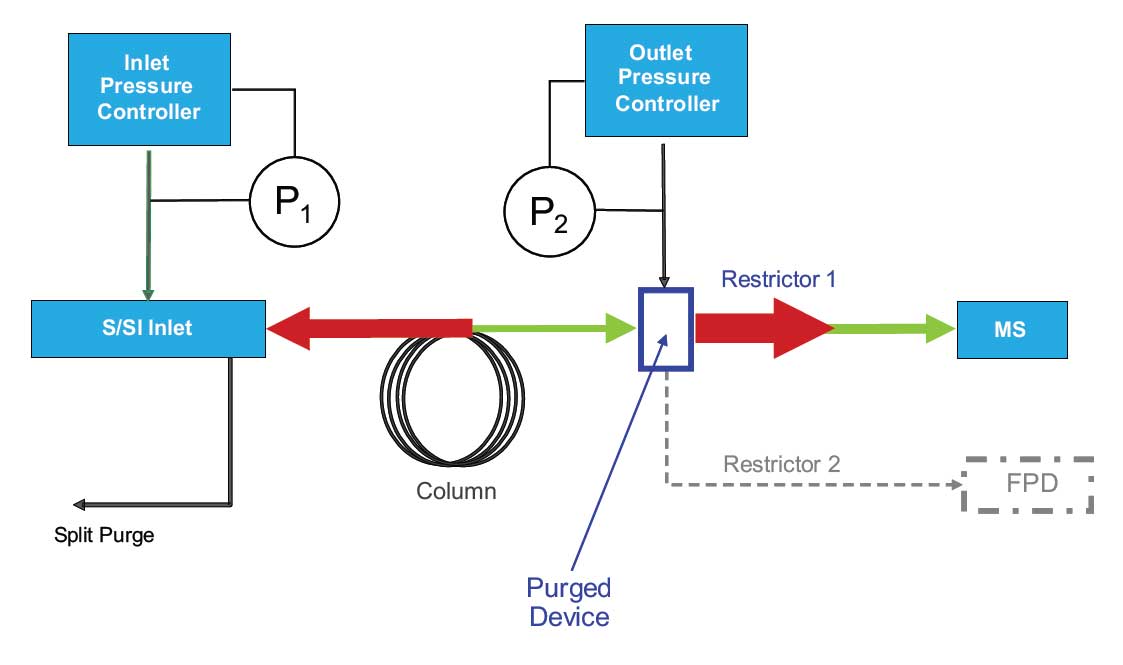
Recall that to backflush a column, the there must be a source of clean carrier gas at the end of the capillary column in order to drive undesirable components back out the head of the column. With packed columns; this is easily achieved through the use of rotary valves to which the packed columns are attached. However rotary valves suffer many issues that make them unsuitable for capillary columns use, the most significant is that the sample is exposed to the rotor material (usually polyimide).
- Dead volumes in connections and valves can cause peak tailing
- Imprecise rotation (the valves can be sticky, adding some variability to rotation initiation)
- Temperature limitations (low and high temperature constraints)
- Sealing surfaces wear in use and leak
- Rotors materials interact with solvents and samples, causing tailing and losses at low concentrations levels)
For backflushing capillary columns, then, low volume devices with inert sample paths are best. Such devices can take many forms and serve many purposes in addition to backflushing the capillary column. Some of those useful for post-column backflushing are:
- Purged effluent splitters (e.g., to split column effluent to several selective detectors, between a detector and a sniff port or sample collector, etc.)
- Devices designed to protect mass spectrometers from air intrusion when changing columns without venting the MS first)
- Simple purged tee (multiple uses including pre-column backflush to be discussed in subsequent articles)
The key requirement is that the device has a controllable source of pressure. This is rather simple to accomplish these days with pressure control devices that electronically control pressures and that are integrated components of the GC. Each manufacturer calls these options by slightly different names but they all provide similar functions. Third-party pressure controllers can be used as can manual pressure regulators with ON/OFF solenoids. However, in all cases, it is prudent to have positive flow through the gas feed leg of the purged device in order to avoid peak tailing and diffusion of sample into the stagnant leg. So, in the case of using a manual pressure controller with ON/OFF solenoid, one must provide a side shunt for some trickle flow around the solenoid. My rule is that the purge flow should be at least 10% of the column flow (a 1 mL/min column flow requires at least 0.1 mL/min purge flow through the device).
When setting up a post-column configuration with a purged device at the end of the capillary column, one should be aware that the head pressure will be different than with the original direct connect configuration. The purged device is adding flow at the end of the column and there usually is a restrictor leading to the detector, so the column outlet pressure will be higher than the original. Connections to mass spectrometers are the most dramatic examples of such a change. In the original direct connection configuration, the end of the column would experience mass spectrometer vacuum (e.g., 5 × 10-5 torr). When using a purged device, the outlet of the column would held slightly above atmospheric pressure during analysis. This several order of magnitude increase in outlet pressure requires an increase in inlet pressure to maintain holdup time and retention times constant. This is not a big issue and is easily accomplished with today’s gas chromatographs following the principles of method translation [2]. Many instruments and GC control software now allow you to specify the outlet pressure and the target holdup time and the inlet pressure will be automatically adjusted for the columns in use.
Picking the optimal restrictor
One picks the post device restrictor based on column flow. Remember that there always must be some flow coming purging through the purged device and that this flow should be at least 10% of the calculated column flow. Follow this general process:
- Calculate the highest expected column flow through the entire analytical method
- for isobaric (constant pressure) methods, the highest flow rate is at the beginning of the run, when the oven temperature is lowest
- for pressure pulse injections, the highest flow rate is during the pressure pulse
- for programmed pressure or flow… you get the picture
- Add 10% to the maximum flow (column flow max × 1.1); this is then the minimum flow that the restrictor must handle
- Select the pressure at which you wish to hold the purged device during analysis. I usually pick something in the 2-4 psig range.
- Determine the temperature at which the restrictor will be held during the run.
- If all of the restrictor is in a mass spectrometer transfer line, it will be isothermal.
- If some of the restrictor is outside the transfer line, I advise that you assume the full length is at the transfer line temperature, this simplifies calculations and ensures that the restrictor flow will always be sufficient
- If all of the restrictor is in the GC oven, then pick the oven temperature corresponding to the highest flow of the analysis (usually the starting oven temperature)
- The diameter of tubing used should be selected such that the length of the restrictor is the minimum practical to handle and configure in the oven. Experience has shown me that this length is at least 30 cm. The diameters I find most useful to have on hand for use as restrictors are 120 µm, 150 µm, 180 µm, and 200 µm. Based on the pressure (this is now the inlet pressure to the restrictor) and temperature from above, the outlet pressure of the restrictor (your detector), and the carrier gas type you are using, calculate the length of deactivated tubing necessary to yield the target flow rate.
The objective is to pick a restrictor that accommodates the maximum column flow, adds at least 10% to avoid tailing, and yet does not add excessive flow, especially when using flow sensitive detectors like mass spectrometers.
Performing a post-column backflush
To accomplish a timely and effective backflush, one uses the time programmable functions of the GC system to do the following at a time soon after the retention time of the last component of interest:
- Hold oven temperature (it has been shown that there is no advantage to continuing the oven temperature ramp, just hold it at the elution temperature of the last component of interest [3])
- Stop data acquisition. No more peaks will elute, so why collect data? Also, when using mass spectrometers, the source is best turned OFF when high flows enter the MS.
- Increase outlet pressure (the higher the better, unless using a flow sensitive detector such as NPD that may need more time to calm down prior to starting the next run, or a mass spectrometer that may have some maximum flow limits)
- Decrease inlet pressure (something slightly above atmospheric is good)
- Make sure that the split vent flow is at least 10% higher than the calculated reversed column flow during backflush
- Backflush for several void volumes; 10 is more than enough if you backflush after each run. (Remember to calculate holdup time under the temperature and pressure conditions of the backflush, just as you do with flow in #5)
Each manufacturer’s GC system will have a slightly different approach to accomplishing the above, and some have wizards in the software to help you through the process. But none is too complicated as long as you keep the above in mind.
If using a post-column splitter, as in Figure 1, then the sum of the flows to each detector would be required to meet the minimum flow requirement. In the case of using a mass spectrometer, I would select the MS restrictor such the MS is operated at its highest S/N, which for many benchtop mass spectrometers is in the 1 – 1.5 mL/min range. Then, select the other restrictor(s) based on the split ratio you wish to achieve between the two detectors.
1. Retention Time Locking is a patented procedure (Agilent Technologies) that matches retention times from one column configuration to another, or as columns length changes as might happen from trimming the column or replacing it with a new one. See reference 2.2. Method Translation and Retention Time Locking in Partition GC, Leonid M. Blumberg and Matthew S. Klee, Anal. Chem., 1998, 70, 3828-38393. Optimizing capillary column backflush to improve cycle time and reduce column contamination, Matthew S. Klee, J. Sep. Sci., 2009, 32, 88–98
This blog article series is produced in collaboration with Dr Matthew S. Klee, internationally recognized for contributions to the theory and practice of gas chromatography. His experience in chemical, pharmaceutical and instrument companies spans over 30 years. During this time, Dr Klee’s work has focused on elucidation and practical demonstration of the many processes involved with GC analysis, with the ultimate goal of improving the ease of use of GC systems, ruggedness of methods and overall quality of results. If you have any questions about this article send them to techtips@sepscience.com